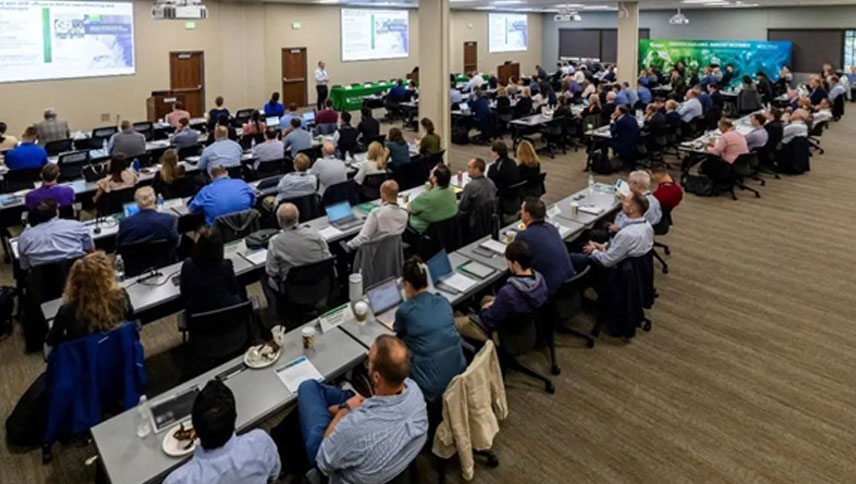
Powder Metallurgy-Hot Isostatic Pressing workshop looks to boost US manufacturing
PM REVIEW
26 Nov 2024
More than 200 stakeholders attended a recent workshop at DOE’s Manufacturing Demonstration Facility to discuss the future of powder metallurgy-hot isostatic pressing as a manufacturing technique (Courtesy Carlos Jones/ORNL, US Department of Energy)
More than 200 delegates attended a recent workshop at the US Department of Energy’s (DOE) Manufacturing Demonstration Facility (MDF) to discuss the future of Powder Metallurgy-Hot Isostatic Pressing (PM-HIP) as a manufacturing technique.
The workshop was organised around seven themes that represent the full PM-HIP value chain: modelling and capsule design; capsule fabrication and preparation; powder production; microstructure properties; large-scale HIP and end customer needs; economics, supply chains and PM-HIP standards; and the voice of the customer.
A steering committee of industry and government stakeholders with firsthand experience using PM-HIP technology provided input on topics. During the workshop, attendees heard from 50 speakers across the entire PM-HIP value chain, a range of voices and perspectives.
“The PM-HIP workshop engaged 200 attendees representing a variety of industry, government and academic stakeholders, including powder manufacturers, researchers, modellers, capsule fabricators, HIP’ers and end-users of components produced through PM-HIP,” stated Dave Gandy, principal technical executive at EPRI and a co-organiser of the workshop. “This workshop has, for the first time, brought together such a diverse community to engage in targeted feedback sessions around the growth and future use of PM-HIP in the US.”
PM-HIP involves placing metal powder in a type of mould known as a capsule, and then exposing it to high temperature and pressure, causing it to fuse into a dense metal component. These components can then be refined to final dimensions and stand up to harsh conditions in demanding applications. ORNL researchers are exploring ways to incorporate advanced manufacturing techniques such as Additive Manufacturing to make the process more efficient and affordable.
“PM-HIP has been used for customised, large-scale aerospace applications, but its use has been limited,” said Soumya Nag, a senior staff scientist in the ORNL Materials Science and Technology Division and the workshop’s organiser. “We believe US manufacturing could benefit by choosing it for more applications, especially nuclear energy generation, concentrated solar power and potentially wind and hydro power.”
ORNL has already been sharing PM-HIP information through the MDF, where researchers have showcased process improvements for making PM-HIP more efficient in terms of cost, material, time and labour.
“We are exploring the feasibility of convergent manufacturing by integrating the flexibility of Additive Manufacturing and the reliability of Powder Metallurgy to fabricate large, complex parts,” Nag added. “We will continue to actively demonstrate and facilitate ways industry can overcome challenges by synergistically coupling experimental and modelling techniques.”
Source: https://www.pm-review.com/powder-metallurgy-hot-isostatic-pressing-workshop-looks-to-boost-us-manufacturing/