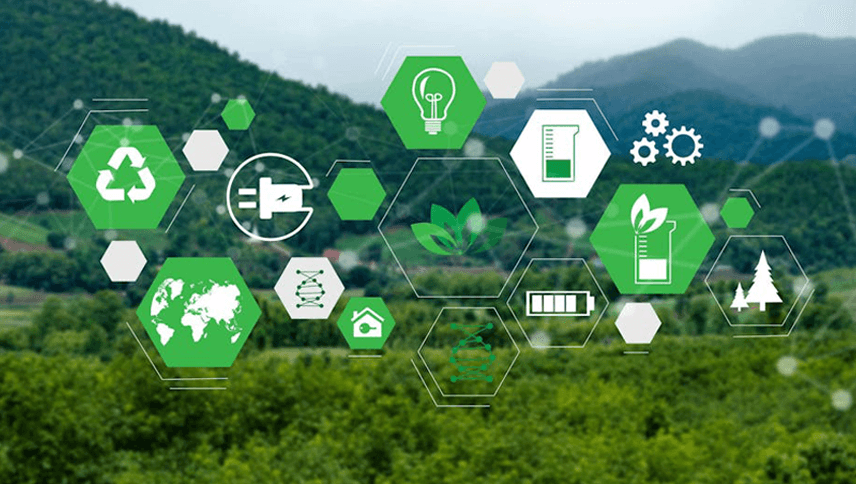
The Rising Influence of Sustainability on Hydraulics and Pneumatics
Power & Motion
By Sara Jensen
Oct. 14, 2024
Sustainability is becoming a larger driver for the design and use of fluid power technologies.
A greater emphasis is being placed on sustainability within the fluid power industry as manufacturers and their customers look to reduce their environmental impact while at the same time achieving performance improvements.
Government regulations being enacted around the world are a driver for the creation and use of more sustainable fluid power technologies as well as companies’ own desire to reduce emissions, material use, and more.
In a recent reader survey conducted by Power & Motion, 78% of respondents said sustainability is influencing their design and use of hydraulics and pneumatics.
A large number of respondents to Power & Motion’s survey see sustainability influencing their design and use of hydraulics and pneumatics.
Christopher Parisse, Senior Controls Product Engineer, Bosch Rexroth, told Power & Motion that sustainability is one of the company’s pillars on which it designs systems. “From a component standpoint, we’re designing our latest generation of pumps and valves to be more efficient, which allows our customers to reap these benefits just by swapping parts out,” he said.
In addition, the company is developing technologies for the production and use of hydrogen, such as its new A4VZA pump to perform hydrogen compression, aiding with the transition to diesel fuel alternatives.
Frank Langro, Director – Product Market Management, Pneumatic Automation, North America at Festo Corp., said that as a company Festo is committed to supporting the Sustainable Development Goals of the United Nations, which set out targets for helping people and the planet.
As such, he said Festo places “a significant focus on the impact of our products on energy usage, both via operation and in [their] production.” In conjunction with this, the company takes into consideration the impact a product will have on sustainability during the product design specification phase.
How Sustainability is Influencing Fluid Power Designs
When asked what percentage of their hydraulic and pneumatic system designs, or use of these technologies, are being influenced by sustainability, almost 36% of respondents said 21% or more are being impacted.
Almost 36% of respondents to a Power & Motion survey indicated that 21% or more of their fluid power technologies, or use of them, are being influenced by sustainability.
The ways sustainability is impacting the fluid power sector are varied. Some respondents said maximizing the lifespan of their products and easing maintenance are how they are incorporating sustainability into their designs. By enabling products to work longer, there is less waste created and fewer materials required to produce a new component.
One respondent noted sustainability is influencing their designs through the use of systems with variable flow pumps, electronic control, and electro-hydraulic proportional valves. These can lead to more precise and efficient operation, helping to minimize energy use and emissions.
Several other respondents noted the development of leak-free systems. This ensures not only efficient operation but also prevents harmful substances, such as hydraulic fluid, from entering the environment.
Use of sensors to monitor pneumatic air consumption and selection of raw materials and performance validation processes were additional methods noted by respondents.
A number of respondents also noted the growing interest from customers in wanting information on the sustainability practices of manufacturers and their suppliers and a general interest from customers in utilizing products considered to be more sustainable.
Of the design changes being made to hydraulics and pneumatics to meet sustainability goals, increasing efficiency was the top choice for survey respondents.
Increasing efficiency is one of the biggest changes being made to hydraulics and pneumatics to meet sustainability goals.
Some additional design changes respondents said they are making include incorporating sensors, better engineering their products, and improving oil purifying solutions.
Hydraulics are known to be a relatively inefficient but powerful technology. As such, this is an area in which many hydraulics manufacturers have been focusing their technology development efforts in recent years because of the energy and emissions savings that can be achieved. It is also becoming increasingly important to the transition to electrification to ensure battery power can last as long as possible between charges.
Parisse said that more and more Bosch Rexroth customers are asking how they can save energy to reduce their carbon footprint. “It’s therefore incumbent on us that our technologies serve as simple ways to integrate with existing machines to achieve substantial sustainability targets,” he said. “Companies are constantly looking for those solutions when they want to make their processes more efficient.”
According to Dr. Andreas Schumacher, Senior Director, Head of Sustainability and Product Compliance at Danfoss Power Solutions, the benefits of efficiency can be broken into three aspects — cost, performance, and sustainability. Higher levels of efficiency lead to fewer losses, creating a more attractive system from a total cost of ownership perspective, he said during a webinar with Power & Motion about efficiency.
In terms of performance, more efficient systems allow you to either do the same amount of work with less energy or do more work with the same amount of energy. For the sustainability aspect, he said fewer losses mean fewer emissions “because you are not burning energy.”
There is also room for efficiency gains in pneumatics. Langro said Festo is bringing more intelligence into its products to enhance efficiency, such as the company’s intelligent air prep series, the MS6E energy-saving modules. “The unit can detect when the machine goes into an idle state and can then maintain a reduced pressure or shut down air to the machine or section of the machine, eliminating excess energy usage due to compressed air leaks,” he explained.
The MS6E energy-saving modules from Festo can detect when a machine goes into an idle state and maintain a reduced pressure or shut down air to the machine to help reduce energy consumption.
In recent years, Langro said Festo has released new products which are lighter in weight to aid with sustainability efforts as well, leading to a reduction in the amount of excess material that might otherwise be used in a product. He provided the example of the company’s compact cylinder ADN-S offering a 48% weight reduction compared to the ISO standard ADN cylinder. “The two-fold advantage here is the lower carbon footprint of the product while meeting the market need of a space-saving, compact footprint,” he said.
The company has also increased the use of re-melted aluminum in its products, to a point that it makes up 78% of annual aluminum usage, said Langro. This helps to reduce the number of raw materials required, which can have several environmental impacts associated with them.
Sustainability Presents Challenges and Opportunities for Fluid Power
Costs were the most common response when asked about the challenges associated with taking sustainability into account for the design and use of fluid power technologies. Many noted the higher initial cost of newer, more sustainable products.
As one respondent pointed out, existing hydraulic and pneumatic components are getting outdated day by day and the present-day components are more advantageous. However, modifications required to replace older technologies with newer options can be difficult and expensive.
Parisse agreed that higher initial costs are typically associated with incorporating sustainability measures, and this can be challenging. “[Adding] extra devices that slow down pumps, monitor pressure feedback, and track insightful data, those all come with an added up-front cost,” he said. “However, when considering sustainability measures, we encourage customers to answer the question, ‘What is the return on the investment?’ ‘How important are these measures to them?’
“We make sure we’re having educated conversations about the positive impacts these solutions can have, including how they ultimately impact a company’s future bottom line.”
The Festo ADN-S pneumatic cylinder weighs 48% less than the standard ISO version, reducing material use and space claim within machines.
Survey respondents noted several other challenges presented by sustainability including:
- resistance from end customers,
- component availability,
- raw material selection and availability,
- compatibility with existing systems,
- considering the entire lifecycle of a product,
- ensuring productivity, maintenance, and other performance attributes.
Langro said it is important to create a balance between employing sustainability and meeting desired performance specifications. In addition, looking at the full “cradle to grave” supply chain for a product is necessary to truly improve sustainability practices. For Festo, this includes an assessment of the most efficient ways to transport products as well as utilizing reusable materials for its product packaging.
The majority of survey respondents, 88%, said they see efforts to be more sustainable as an opportunity for the hydraulics and pneumatics industry.
The majority of respondents to a Power & Motion survey said they see sustainability as an opportunity for the fluid power industry.
Several respondents said sustainability provides the chance to create new products and integrate advanced technologies such as IoT (Internet of Things). There are also emerging market opportunities such as the production of hydrogen.
Many also noted the benefits that will be achieved through more sustainable fluid power solutions such as reducing energy consumption and service needs. One respondent noted that “hydraulics are still the most efficient way of transferring energy (in terms of power density). But in order to keep hydraulics alive we must keep [increasing the] overall efficiency of hydraulic systems.”
Both Parisse and Langro agree that sustainability offers opportunities for the fluid power industry.
For Bosch Rexroth, this includes more solutions based on its Sytronix technology which utilizes variable-speed pump drives to save energy and reduce noise. Parisse said it enables pump efficiency to be optimized and provide energy on demand. “With eco-friendly solutions, every drop of energy that’s put in, you’ll get more out.”
Hydraulic circuit design will be an important aspect going forward as more solutions for sustainability will be considered from the ground up. This will lead to more efficient pumps, less throttling across valves, and reduced oil use.
Bosch Rexroth’s CytroPac and CytroBox incorporate its Sytronix technology comprised of a variable-speed pump drive which aids with energy savings and noise reductions.
“We’ve seen that with our CytroPac and CytroBox — they use a quarter of the oil as a traditional power unit,” he said. “In general, the less oil that’s used in any solution, the better. We see that continuing in the future along with an increased use of electronics and greater incorporation of sustainability measures in the design of hydraulic circuits.”
“I believe that change always creates opportunity. As the users of fluid power request higher levels of sustainability in their machine operation and decreased carbon footprint of the items in their machines, this will require further innovative products and solutions,” concluded Langro.
Source: https://www.powermotiontech.com/hydraulics/article/55150495/the-rising-influence-of-sustainability-on-hydraulics-and-pneumatics